While jelly-filled (or gel-filled) cables offer many advantages, they also present some unique challenges in maintenance. Here’s an overview of the main challenges in maintaining jelly-flooded cables:
1. Gel Compound Degradation:
Over time, the gel compound can degrade, especially when exposed to extreme temperatures or environmental factors. This degradation can lead to:
– Reduced moisture protection
– Potential leakage of the compound
– Changes in the cable’s electrical properties
2. Difficulty in Repairs:
When repairs are necessary, working with gel-filled cables can be more challenging:
– The gel needs to be cleaned from the cable ends before splicing
– Special tools and techniques may be required to properly clean and prepare the cable
– Re-sealing the cable after repairs to maintain its moisture barrier can be complex
3. Weight and Handling:
Gel-filled cables are generally heavier than their air-core counterparts:
– This can make installation and replacement more labor-intensive
– It may require stronger support structures in aerial installations
4. Temperature Sensitivity:
The viscosity of the gel compound can change with temperature:
– In cold temperatures, the gel may become too stiff
– In hot temperatures, it might become too fluid and potentially leak
5. Environmental Concerns:
While modern gel compounds are often designed to be more environmentally friendly, there are still concerns:
– Proper disposal of old cables can be more complicated
– Some older gel compounds may contain harmful substances
6. Compatibility Issues:
When integrating gel-filled cables into existing networks:
– There may be compatibility issues with connectors or equipment designed for air-core cables
– Special transition points might be needed where gel-filled and air-core cables meet
7. Inspection Challenges:
Visual inspection of the cable core is more difficult:
– The gel can obscure visual cues that might indicate damage or wear
– Advanced diagnostic tools may be required for thorough inspections
8. Cost of Maintenance:
While gel-filled cables often have lower long-term maintenance costs, when maintenance is required:
– The materials and equipment needed can be more expensive
– The process can be more time-consuming, potentially increasing labor costs
9. Training Requirements:
Maintenance teams need specialized training:
– To handle the unique properties of gel-filled cables
– To use specific tools and techniques for working with these cables
10. Gel Migration:
In some cases, especially with older or poorly manufactured cables:
– The gel compound can migrate along the cable
– This can lead to uneven protection and potential issues at termination points
Would you like me to elaborate on any specific aspect of these challenges?
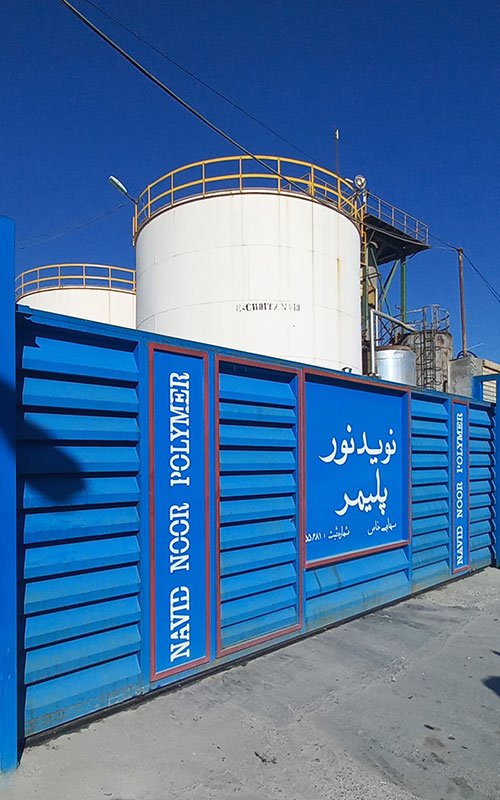
This is Kamran Malekian working in the petroleum jelly manufacturing industry for Navid Noor Company since 2013 I am eager to make content in this industry and have a good impact on professional users and people using cosmetic and pharmaceutical products.
No comment