Detecting jelly leakage or loss in installed cables is crucial for maintaining the integrity and performance of cable systems, especially in outdoor or harsh environments. Here are several methods and techniques used for detecting jelly leakage or loss in installed cables:
1. Visual Inspection:
– Regular visual checks for signs of jelly seepage at cable ends, joints, or damaged areas.
– Look for discoloration or staining on cable jackets that might indicate jelly leakage.
– Inspect termination points and connectors for signs of gel.
2. Tactile Examination:
– Physically feel the cable jacket for soft spots or areas that feel less firm, which could indicate jelly loss.
– Check for sticky residue on the outer jacket, which might suggest leakage.
3. Electrical Testing:
– Capacitance Testing: Changes in capacitance can indicate jelly loss or water ingress.
– Insulation Resistance Testing: Decreased resistance might suggest jelly loss and moisture penetration.
– Time Domain Reflectometry (TDR): Can detect changes in cable characteristics that might indicate jelly loss.
4. Moisture Detection:
– Use moisture meters designed for cable testing to detect increased moisture levels.
– Look for corrosion or oxidation on metallic components, which can indicate moisture ingress due to jelly loss.
5. Pressure Testing:
– For pressurized cable systems, monitor pressure levels. A pressure drop could indicate jelly loss.
– Conduct gas flow tests to detect leaks in the cable sheath.
6. Thermal Imaging:
– Use infrared cameras to detect temperature variations along the cable length, which might indicate areas of jelly loss.
– Jelly-filled sections typically have different thermal properties compared to sections with jelly loss.
7. Ultrasonic Testing:
– Use ultrasonic equipment to detect voids or changes in cable density that might indicate jelly loss.
– Particularly useful for larger cables or those in conduits.
8. X-ray Inspection:
– For critical installations, portable X-ray equipment can be used to visualize the internal structure of cables and detect jelly loss.
9. Weight Analysis:
– In some cases, weighing sections of cable (if accessible) can indicate jelly loss compared to known specifications.
10. Chemical Detection:
– Use chemical detection methods to identify the presence of jelly compounds on the outer surface of the cable.
– Some specialized detectors can sense vapors from jelly compounds.
11. Acoustic Testing:
– Use acoustic reflectometry to detect changes in the cable’s acoustic properties, which can indicate jelly loss or water ingress.
12. Distributed Temperature Sensing (DTS):
– For fiber optic cables, DTS can detect temperature variations that might indicate jelly loss and subsequent moisture ingress.
13. Partial Discharge Testing:
– Detect partial discharges that might occur due to voids created by jelly loss.
14. Cable Radar Systems:
– Advanced systems use radar technology to detect changes in cable properties along its length.
15. Sampling:
– In some cases, taking small samples from accessible points can help assess jelly condition.
– This is more invasive and typically used only when other methods are inconclusive.
16. Monitoring Systems:
– Install permanent monitoring systems that continuously check for changes in cable properties.
– These can provide early warnings of jelly loss or degradation.
17. Historical Data Analysis:
– Compare current test results with historical data to identify trends that might indicate progressive jelly loss.
18. Environmental Monitoring:
– Monitor the environment around the cable for conditions that might accelerate jelly loss (e.g., extreme temperatures, and chemical exposure).
Considerations:
1. Safety: Ensure all testing methods comply with safety regulations, especially when working with live cables.
2. Non-Destructive Testing: Prioritize non-destructive testing methods to maintain cable integrity.
3. Accessibility: Consider the accessibility of the cable when choosing detection methods.
4. Cable Type: Different detection methods may be more suitable for specific cable types (e.g., power cables vs. telecommunications cables).
5. Environmental Factors: Account for environmental conditions that might affect test results.
6. Frequency of Inspection: Establish a regular inspection schedule based on the cable’s criticality and environmental exposure.
7. Documentation: Maintain detailed records of all inspections and test results for trend analysis.
8. Expertise: Ensure personnel conducting tests are properly trained and equipped.
9. Combination of Methods: Often, a combination of detection methods provides the most comprehensive assessment.
10. Cost-Benefit Analysis: Balance the cost of detection methods against the potential cost of cable failure.
By implementing a comprehensive detection strategy, cable operators can identify jelly loss or leakage early, preventing more serious cable failures and maintaining system reliability. The choice of detection methods should be based on the specific cable system, its environment, and operational requirements.
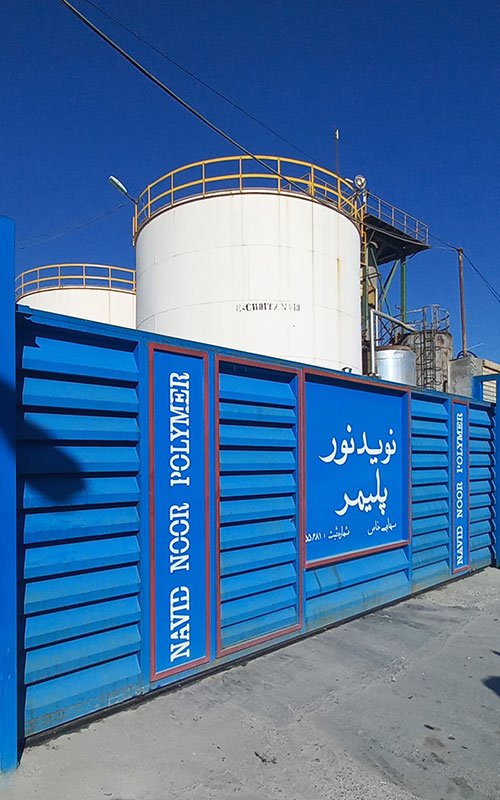
This is Kamran Malekian working in the petroleum jelly manufacturing industry for Navid Noor Company since 2013 I am eager to make content in this industry and have a good impact on professional users and people using cosmetic and pharmaceutical products.
No comment