Installing jelly-filled cables requires careful planning and execution to ensure optimal performance and longevity. Here are the key installation considerations for jelly-filled cables:
1. Environmental Factors:
– Temperature: Consider ambient temperature during installation. Extreme temperatures can affect jelly viscosity.
– Moisture: Protect cable ends from moisture ingress during installation.
– UV Exposure: Minimize exposure to direct sunlight, which can degrade cable jackets.
2. Handling and Preparation:
– Proper Unspooling: Use appropriate equipment to prevent cable twisting or kinking.
– Bend Radius: Adhere to manufacturer-specified minimum bend radius to avoid damage.
– Cable Ends: Properly seal cable ends to prevent jelly leakage or contamination.
3. Pulling Techniques:
– Lubricants: Use compatible cable lubricants to reduce friction during pulls.
– Pulling Tension: Monitor and stay within the specified maximum pulling tension.
– Continuous Pulls: Avoid stopping during long pulls to prevent jelly settling.
4. Conduit and Duct Considerations:
– Size: Ensure adequate conduit size for the cable diameter plus jelly.
– Cleanliness: Clean conduits before installation to remove debris.
– Fill Ratio: Adhere to proper conduit fill ratios, considering jelly volume.
5. Direct Burial:
– Soil Conditions: Assess soil type and prepare trenches appropriately.
– Depth: Install at proper depth to protect from physical damage and temperature fluctuations.
– Backfill: Use appropriate backfill material to avoid cable damage.
6. Aerial Installation:
– Tension: Properly tension cables to avoid sagging while preventing overstress.
– Attachment Points: Use appropriate hardware that doesn’t damage the cable jacket.
– Drip Loops: Incorporate drip loops to prevent water ingress at connection points.
7. Splicing and Termination:
– Jelly Removal: Properly clean cable ends before splicing or termination.
– Sealing: Use appropriate methods to seal splices and prevent jelly leakage.
– Compatibility: Ensure splice and termination materials are compatible with the jelly compound.
8. Temperature Considerations:
– Installation Temperature: Install within manufacturer-specified temperature range.
– Thermal Expansion: Allow for cable expansion and contraction in different temperatures.
9. Vertical Runs:
– Support: Provide adequate support to prevent jelly migration in vertical installations.
– Transition Points: Pay special attention to horizontal-to-vertical transition points.
10. Testing:
– Pre-Installation: Conduct tests to ensure cable integrity before installation.
– Post-Installation: Perform thorough testing after installation to verify performance.
11. Documentation:
– Route Mapping: Accurately document cable routes and splice locations.
– Test Results: Record all pre- and post-installation test results.
12. Safety Precautions:
– PPE: Use appropriate personal protective equipment when handling jelly-filled cables.
– MSDS: Have Material Safety Data Sheets available for the jelly compound.
13. Equipment Considerations:
– Compatibility: Ensure all installation equipment is compatible with jelly-filled cables.
– Cleaning: Properly clean equipment after use to prevent jelly contamination.
14. Storage:
– Conditions: Store cables in appropriate conditions before installation.
– Sealing: Keep cable ends sealed during storage to prevent contamination.
15. Pressure Systems:
– For pressurized systems, ensure proper sealing and pressure testing.
– Install pressure monitoring systems as required.
16. Future Access:
– Plan for future maintenance access, especially in buried or encased installations.
17. Jelly Characteristics:
– Understand the specific properties of the jelly used, including its behavior in different temperatures.
18. Cable Identification:
– Properly label cables, including information about the jelly compound for future reference.
19. Training:
– Ensure installation personnel are trained in handling jelly-filled cables.
20. Regulatory Compliance:
– Adhere to local codes and standards for cable installation.
21. Environmental Impact:
– Consider the environmental impact of jelly compounds, especially in sensitive areas.
22. Post-Installation Care:
– Implement a maintenance plan that includes regular inspections for jelly leakage or degradation.
Best Practices:
1. Consult manufacturer guidelines for specific installation requirements.
2. Conduct a site survey to identify potential installation challenges.
3. Develop a detailed installation plan, including contingencies for potential issues.
4. Use experienced personnel familiar with jelly-filled cable installation.
5. Implement quality control measures throughout the installation process.
6. Consider future expansion needs when planning cable routes and spare capacity.
7. Maintain open communication with cable manufacturers for technical support.
By carefully considering these factors, installers can ensure that jelly-filled cables are properly installed, maximizing their performance and lifespan. Proper installation is crucial for maintaining the integrity of the jelly filling and ensuring the cable’s protective and performance characteristics are preserved throughout its operational life.
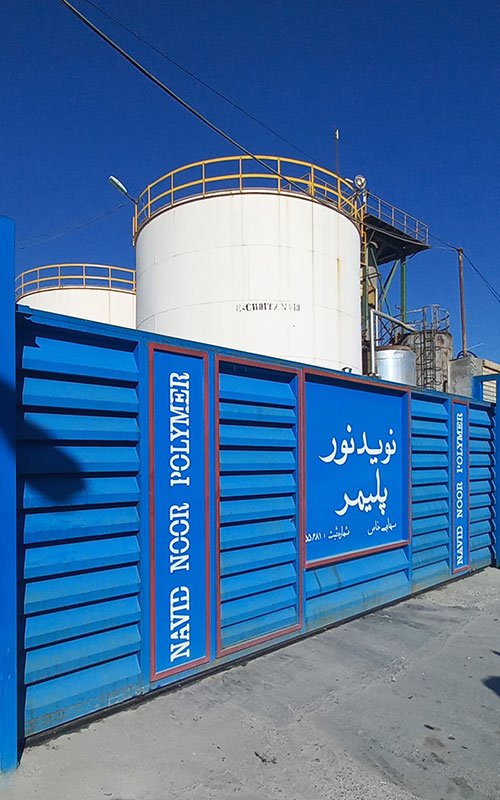
This is Kamran Malekian working in the petroleum jelly manufacturing industry for Navid Noor Company since 2013 I am eager to make content in this industry and have a good impact on professional users and people using cosmetic and pharmaceutical products.
No comment