Micro Wax: Boosting powder coatings’ performance
Introduction
An adaptable ingredient in powder coatings, micro wax significantly improves performance, durability, and appearance. Its special characteristics help powder coatings improve flow, leveling, and surface qualities, therefore producing better finishes for many different uses. This all-inclusive book provides insightful analysis of the advantages, uses, and methods of using micro wax in powder coatings, therefore benefiting manufacturers, formulators, and coating experts.
Clarifying Micro Wax
Usually ranging in particle size from 3 to 10 microns, micro wax—also known as synthetic wax or polyethylene wax—is a finely split wax. Derived from petroleum feedstocks, it undergoes sophisticated refining techniques to acquire the appropriate qualities for many industrial uses, including powder coatings.
Significance of powder coatings
Because of their environmental advantages, durability, and simplicity, powder coatings are a common surface finishing alternative. Perfect for industrial, architectural, and automotive uses, they provide great corrosion resistance, chemical resistance, and ornamental qualities.
Micro Wax Properties
Micro wax’s main qualities that fit for powder coatings are:
Microwax particles have a homogeneous size distribution that facilitates consistent dispersion and enhances coating qualities.
Micro wax’s low molecular weight helps it to be readily incorporated into powder coating recipes without changing viscosity or flow characteristics.
Microwax melts at rather low temperatures during the curing process, therefore encouraging flow and powder-coating film development.
Microwax serves as an internal lubricant inside the powder coating matrix, therefore lowering friction between particles and enhancing coating integrity and adherence.
Uses in Powder Coatings
In powder coatings, micro wax finds many uses including:
Micro wax enhances the flow and leveling of powder coatings, therefore producing a smooth, homogeneous layer and less orange peel or surface flaws.
Micro wax gives powder coatings robust defense against abrasion and mechanical damage, therefore improving their scratch and mar resistance.
Micro wax may be used to powder coatings to provide textured or matte finishes, therefore giving covered surfaces depth, richness, and tactile appeal.
Micro wax helps powder coatings to be more heat stable and thermally resistant, therefore enabling their capacity to tolerate high temperatures during curing and service.
Methods for Using Micro Wax
Think through the following methods when adding micro wax to powder coatings:
Before extrusion or mixing to guarantee consistent dispersion and compatibility, pre-blend micro wax with other powder coating components including resins, colors, and additives.
To prevent early melting or agglomeration, add micro wax to the powder coating formulation once the main components have been blended or distributed.
To maximize the dispersion and distribution of micro wax within the powder coating matrix, change processing variables like temperature, mixing speed, and residence time.
Case Studies: Micro Wax under Use
Automotive Coatings
Micro wax is included in vehicle coatings by a powder coating producer to enhance flow, leveling, and scratch resistance. They fulfill strict performance criteria for automotive uses by adjusting the micro wax concentration and processing conditions, therefore generating powder coatings with smooth, glossy surfaces and increased durability.
Architectural Finish Notes
Micro wax in textured powder coatings is used in the architectural coatings industry for external surfaces and building facades. Changing the particle size and form of the micro wax particles produces powder coatings with distinctive textures, patterns, and visual effects, thereby improving the aesthetic appeal and weather resistance of architectural buildings.
Industrial Coatings
An industrial coatings producer improves the performance of powder coatings derived from epoxy for machinery and heavy-duty equipment. Micro wax is an internal lubricant that enhances the flow, leveling, and impact resistance of the powder coatings therefore guaranteeing long-lasting protection and corrosion resistance in demanding industrial situations.
Advantages of Micro Wax
Micro wax has various advantages for powder coatings:
Microwax reduces surface flaws and improves the look of powder coatings by encouraging consistent, smooth film development.
Micro wax improves scratch, mar, and abrasion resistance, therefore offering robust defense against wear and tear in many uses.
Micro wax gives powder coatings the ability to create textured, matte, or glossy surfaces, therefore providing variation and customizing choices for many substrates and design criteria.
Micro wax helps to be easily included in powder coating formulas, therefore boosting processing efficiency and lowering production costs.
Safety Thoughts
Although micro wax is usually regarded as acceptable for use in powder coatings, it is important to take the following safety issues under observation:
When handling micro wax powder, use suitable respiratory protection—such as dust masks or respirators—to stop inhalation of airborne particles.
Steer clear of extended skin contact with micro wax granules; after handling, properly wash your hands to avoid sensitizing or irritation.
Install local exhaust ventilation or dust collecting devices to reduce airborne dust exposure during the handling and processing of micro wax powder.
Store micro wax powders in sealed containers in a cool, dry environment far from heat sources and ignition dangers; practice safe handling techniques to avoid mishaps or spills.
Future Developments and Novelties
Future trends and developments in micro wax use might include as powder coating technology develops:
Development of nanostructured micro wax additives with improved dispersion, surface activity, and performance advantages for powder coatings
Formulation of micro wax additives with functional groups or surface modifiers to provide powder coatings particular qualities, including self-cleaning, antibacterial, or anti-corrosive properties, from which to derive.
Research of bio-based or renewable sources for micro wax manufacture provides sustainable substitutes with less carbon footprint and environmental effects.
Integration of smart coatings with micro wax additives for self-healing, self-cleaning, or corrosion-sensing purposes improves the performance and usefulness of powder coatings in many uses.
Recommendations and Final Thought
Offering advantages like enhanced flow, leveling, scratch resistance, and textural diversity, micro wax is essential in boosting the performance, longevity, and appearance of powder coatings. Understanding its characteristics, uses, and safety issues helps powder coating producers and formulators maximize micro wax’s possibilities to produce high-performance coatings for industrial, architectural, and automotive uses.
Discover how adding micro wax to your powder coating recipes could improve performance, longevity, and appearance. Experiment with many formulas, processing conditions, and application processes to maximize the performance of your powder coatings and satisfy the changing demands of your consumers.
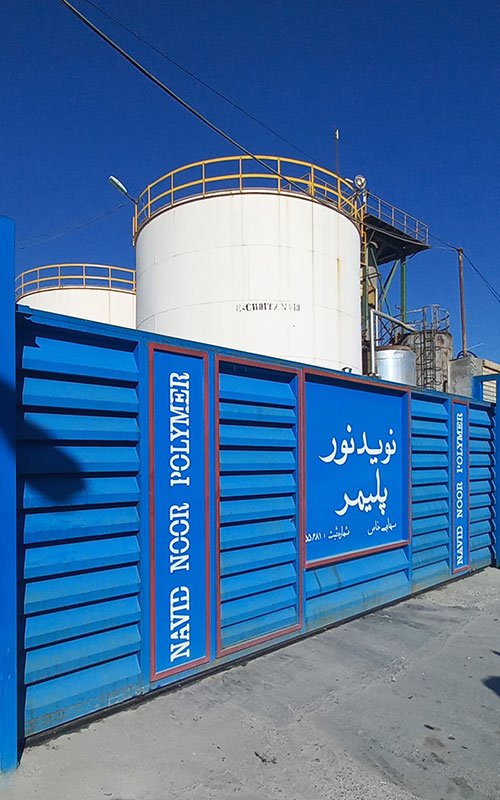
This is Kamran Malekian working in the petroleum jelly manufacturing industry for Navid Noor Company since 2013 I am eager to make content in this industry and have a good impact on professional users and people using cosmetic and pharmaceutical products.
No comment