Quality control in cable jelly production is a critical aspect of ensuring the reliability and performance of jelly-filled cables. Let’s explore the key elements of quality control in this process:
1. Raw Material Testing:
– Chemical Composition: Verify the purity and composition of raw materials.
– Viscosity Testing: Ensure base materials meet specified viscosity ranges.
– Contamination Checks: Test for unwanted particles or impurities.
2. Mixing Process Control:
– Temperature Monitoring: Maintain optimal temperature during mixing.
– Mixing Time: Control the duration to ensure proper blending.
– Homogeneity Testing: Check for uniform distribution of components.
3. Viscosity Control:
– Regular Sampling: Test viscosity at various stages of production.
– Temperature-Viscosity Relationship: Verify consistency across temperature ranges.
– Shear Testing: Assess how viscosity changes under different shear rates.
4. Water Resistance Testing:
– Water Penetration Tests: Ensure the gel effectively blocks water.
– Hydrophobicity Measurements: Check the gel’s water-repelling properties.
– Long-term Immersion Tests: Assess performance over extended periods in water.
5. Electrical Property Testing:
– Dielectric Strength: Measure the gel’s insulating properties.
– Volume Resistivity: Ensure high electrical resistance.
– Dielectric Constant: Verify consistency with cable design requirements.
6. Chemical Stability Tests:
– Oxidation Resistance: Check for stability against oxidation.
– pH Testing: Ensure the gel maintains a neutral pH to avoid cable corrosion.
– Compatibility Tests: Verify no adverse reactions with cable materials.
7. Thermal Performance:
– High-Temperature Stability: Test performance at elevated temperatures.
– Low-Temperature Flexibility: Ensure the gel remains effective in cold conditions.
– Thermal Cycling: Assess stability through temperature fluctuations.
8. Mechanical Property Testing:
– Penetration Tests: Measure gel consistency and firmness.
– Adhesion Tests: Check how well the gel adheres to cable materials.
– Drip Tests: Ensure the gel doesn’t flow or separate at high temperatures.
9. Aging Tests:
– Accelerated Aging: Simulate long-term performance in a shorter timeframe.
– UV Resistance: Test stability when exposed to ultraviolet light (for some applications).
– Environmental Stress Testing: Assess performance under various environmental conditions.
10. Batch Consistency:
– Batch-to-Batch Variation Analysis: Ensure consistency across production runs.
– Statistical Process Control: Implement SPC techniques to monitor production stability.
11. Contamination Control:
– Particulate Analysis: Check for unwanted solid particles.
– Filtration Efficiency: Verify the effectiveness of filtration systems.
12. Rheological Testing:
– Flow Behavior Analysis: Understand how the gel flows under different conditions.
– Thixotropy Testing: Assess the gel’s ability to change viscosity under stress.
13. Environmental and Safety Compliance:
– VOC (Volatile Organic Compound) Testing: Ensure compliance with environmental regulations.
– Toxicity Testing: Verify the gel meets safety standards for handling.
14. Application-Specific Testing:
– Cable Filling Tests: Verify the gel’s performance when applied to actual cables.
– Pressure Resistance: For submarine cable applications, test under high pressure.
15. Documentation and Traceability:
– Batch Records: Maintain detailed records of each production batch.
– Raw Material Traceability: Implement systems to trace raw materials through production.
16. Continuous Improvement:
– Process Capability Studies: Regularly assess and improve production capabilities.
– Customer Feedback Integration: Incorporate field performance data into quality processes.
17. Quality Management System:
– ISO 9001 Compliance: Adhere to international quality management standards.
– Regular Audits: Conduct internal and external audits of the production process.
18. Shelf Life Testing:
– Storage Stability: Assess how the gel properties change over time in storage.
– Packaging Integrity: Ensure packaging maintains gel quality during storage and transport.
Quality control in cable jelly production is a comprehensive process that involves multiple stages of testing and monitoring. It requires a combination of chemical, physical, and electrical testing to ensure that the final product meets the stringent requirements for use in cable manufacturing. The goal is to produce a consistent, high-quality cable gel that will provide reliable performance throughout the cable’s lifespan, often under challenging environmental conditions.
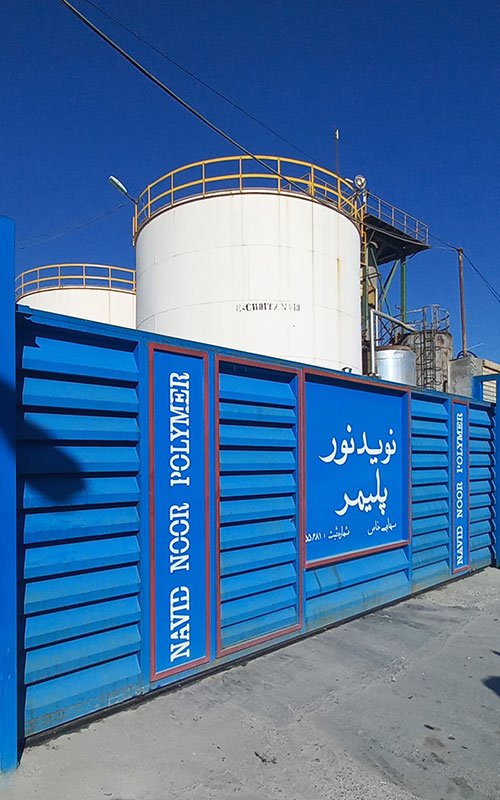
This is Kamran Malekian working in the petroleum jelly manufacturing industry for Navid Noor Company since 2013 I am eager to make content in this industry and have a good impact on professional users and people using cosmetic and pharmaceutical products.
No comment